Zwarte, blauwe, rode en soms groene. Dan heb je de variatie in inkt wel zo’n beetje gehad. Als het om balpennen gaat misschien, want inkt kom je vaker tegen dan je denkt. NEMO Kennislink bracht een bezoek aan BASF in Heerenveen en ontdekte wat je eigenlijk ziet als je naar een bedrukte verpakking kijkt.
Eerst maar een bekentenis: ik dacht eigenlijk nooit zoveel na over inkt. Het is typisch zo’n product dat je niet bewust opmerkt. Je ziet letters en vormen, maar de inkt zelf? Sinds een bezoek aan chemiebedrijf BASF in Heerenveen is dat allemaal veranderd. Nu kijk ik naar de bedrukking op een pak vruchtenyoghurt of een zak chips en zie ik bindmiddelen, additieven en pigmenten die samen een extreem dun en toch hard laagje vormen. Want inkt is een mengsel van verschillende bestanddelen, zo weet ik nu. En in Heerenveen onderzoeken, verbeteren en maken ze twee van die bestanddelen.
Bij een groot bedrijf als BASF (spreek uit: B A S F en niet Bas F) ontkom je niet aan intimiderende getallen. Vestigingen in meer dan tachtig landen, ruim 120.000 werknemers, een omzet van meer dan zeventig miljard en productievolumes van miljoenen kilo’s per jaar. Toch merk je daar bij BASF Heerenveen niets van. Je ziet geen grote fabrieken met een wirwar aan buizen, geen hoge hekken met bewaking en slagbomen, maar een gewoon bedrijfspand op een standaard bedrijventerrein net buiten de bebouwde kom.
Vanaf het station fiets je er zo naartoe. Dat doen de meeste bezoekers overigens niet, maak ik op uit het ontbreken van een fietsenstalling bij de ingang. “Ben je op de fiets?”, reageert mijn gastheer Arjan Termaten enigszins verbaasd. “Oh, meestal halen wij mensen even met de auto van het station.” Aha, iets om te onthouden voor als het eens minder mooi weer is dan vandaag.
Cornflakes of koekjes?
Heerenveen is BASF’s Europese hoofdvestiging als het gaat om producten voor Printing & Packaging. “We ontwikkelen en produceren hier bindmiddelen voor inkt”, vertelt Termaten. Hij geeft leiding aan een team van zestien mensen dat zich bezighoudt met productontwikkeling. Daarvoor ben ik gekomen, want ik vraag me af wat je nog kunt ontwikkelen aan de ingrediënten van inkt? Een heleboel, zo wordt al snel duidelijk. De ene inkt is de andere niet. De inkt die wordt gebruikt om een kartonnen doos cornflakes te bedrukken is niet dezelfde als die je gebruikt voor de kunststofwikkel om een rol koekjes of het etiket van een bierflesje.
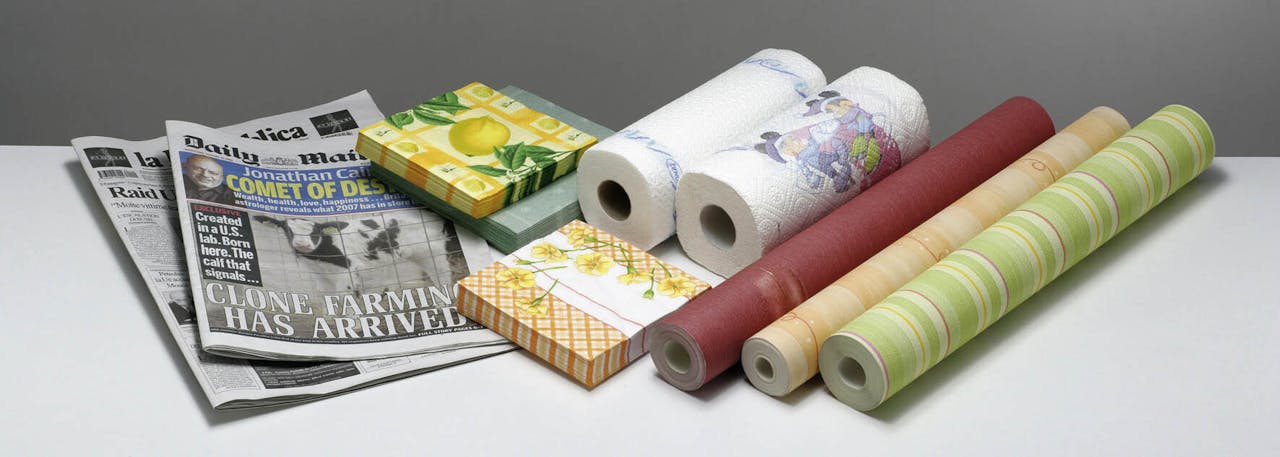
Dat een krant gedrukt wordt met inkt is een inkopper. Maar ook servetten, cadeaupapier en decoratieve keukenrollen danken hun kleuren en patronen aan inkt.
BASFDat verklaart het grote assortiment aan bestanddelen dat ze in Heerenveen maken, zegt Mark van den Brink. Hij is hoofd van de afdeling die verantwoordelijk is voor alles wat te maken heeft met de productieprocessen. “We leveren ongeveer tweehonderd verschillende producten. Dat is een grote groep, maar ieder product moet precies zijn afgestemd op de uiteindelijke toepassing. Het materiaal waar de verpakking uit bestaat speelt een rol, net als de manier waarop de verpakking wordt bedrukt. Veel van onze producten worden gebruikt op de verpakking van voeding en dranken, dus daar komen nog weer extra eisen bij kijken.”
Maar dan nog blijft de vraag staan waarom er doorlopend onderzoek en ontwikkeling nodig is. Veranderen de verpakkingen? Wil de klant steeds weer iets nieuws? Heeft het te maken met duurzaamheid? Met de mogelijkheden voor recycling van de verpakking? Of met nieuwe veiligheidseisen? Het antwoord op al deze vragen is ‘ja’. Van heel veel verschillende kanten komen er nieuwe eisen en wensen die in stapjes terechtkomen bij de productontwikkelaars van BASF.
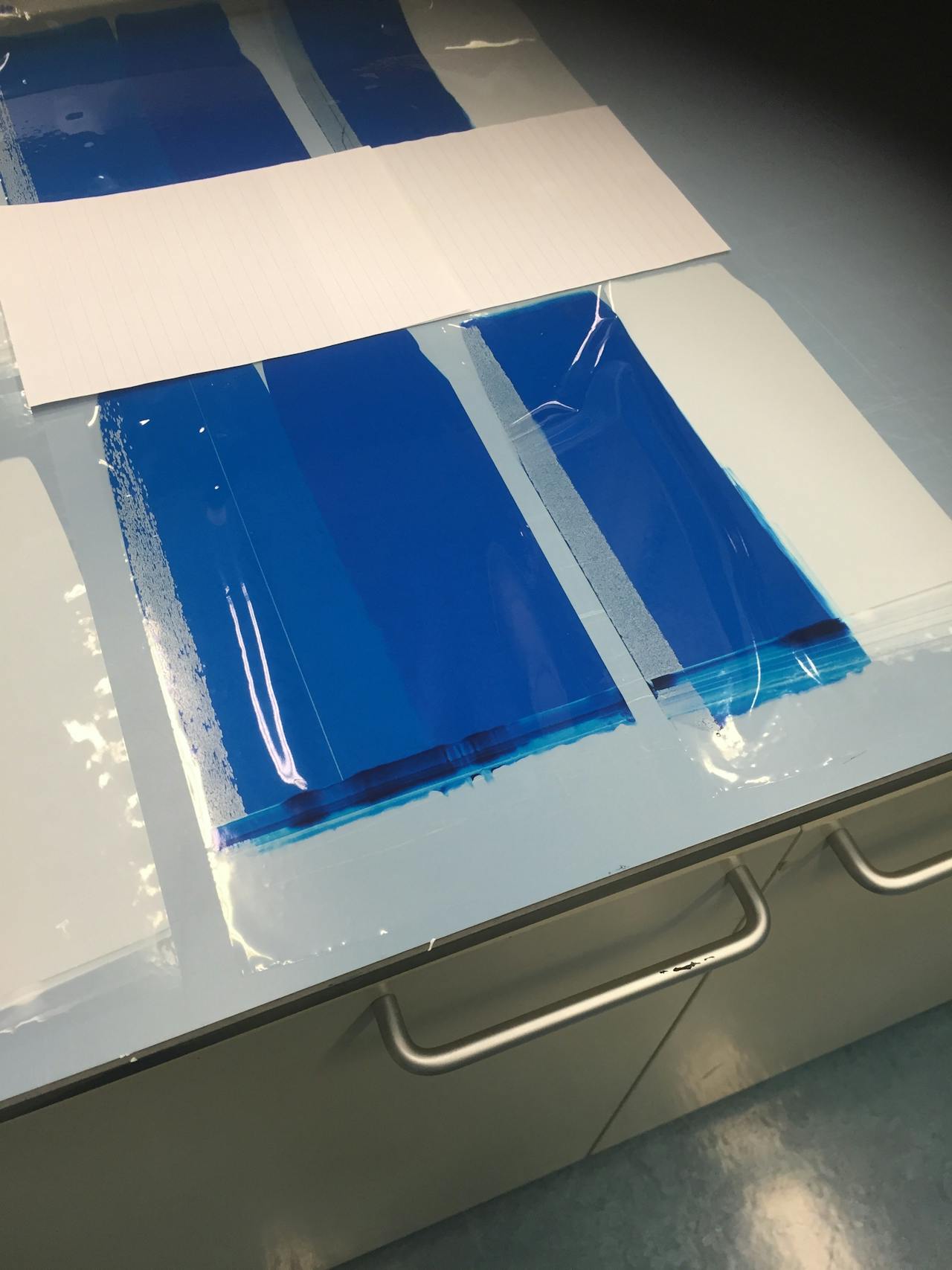
Verschillende bindmiddelen gemengd met blauw pigment. De inkt wordt op een een transparant folie uitgerold om te beoordelen hoe de kleur zich houdt en, door de massa te bepalen, hoe dik de laag inkt wordt.
Esther Thole voor NEMO KennislinkTermaten geeft een voorbeeld. “Onze belangrijkste afnemers zijn de bedrijven die inkt maken. Zij leveren weer aan de drukkers. Als daar een probleem ontstaat of een drukker stapt over naar een nieuwe type drukpers waar de oude inkt niet lekker in loopt, dan komen die problemen en wensen via de inktproducent weer bij ons terecht.” Een andere belangrijke bron van werk voor de ontwikkelaars vormen veranderingen in de wet- en regelgeving. Een bepaalde grondstof is niet langer toegestaan bijvoorbeeld. Daar moet een alternatief voor worden gezocht en dat betekent vaak dat je het hele product en het proces moet aanpassen.
Bindmiddel
De nieuwe wensen van afnemers of nieuwe eisen die de overheid oplegt komen vaak terecht op het bord van chemicus Gerald Metselaar, een van de drie Product Development Scientists in het team van Termaten. Aan hem en zijn collega’s de taak om uit te zoeken wat ze kunnen veranderen aan de ingrediënten om een inkt te leveren met de gewenste eigenschappen.
Inkt bestaat uit vier onderdelen: oplosmiddel, bindmiddel, pigment en, voor speciale eigenschappen, additieven. Het oplosmiddel zorgt ervoor dat de inkt vloeibaar blijft tijdens de verwerking, maar verdampt snel nadat de inkt is opgebracht zodat de inkt droogt. Bij BASF werken ze uitsluitend met water als oplosmiddel voor de bindmiddelen, waarmee meteen punten worden gescoord als het gaat om duurzaamheid en om veiligheid voor de mensen die met de inkt werken.
Het betekent ook dat aan het oplosmiddel niets te sleutelen valt. Die eer gaat naar het bindmiddel, daar valt juist veel aan te veranderen. “Het bindmiddel vormt de feitelijke coating, het harde dunne laagje”, legt Metselaar uit. “Het pigment geeft de kleur, maar die kleur wordt door het bindmiddel vastgehouden.” De bindmiddelen die BASF ontwikkelt bestaan uit heel kleine bolletjes polymeren – lange ketens aan elkaar gekoppelde moleculen. Polymeren noemen we in het dagelijks leven vaak kunststoffen.
Nanobolletjes
De bolletjes zijn ongeveer honderd nanometer (een nanometer is een miljardste meter) groot. Ze lossen niet op in water, maar zweven daarin rond. Daarom spreken ze hier van een ‘watergedragen’ bindmiddel. Metselaar legt uit hoe dat werkt. “Als je zo’n watergedragen bindmiddel in een heel dun laagje opbrengt, verdampt het water. De bolletjes komen daardoor met elkaar in contact en versmelten dan tot een geheel, een blijvend harde, dunne laag.” Je kunt de eigenschappen van het bindmiddel aanpassen door andere bouwstenen van de polymeren in de bolletjes te kiezen. “Daarmee kunnen we beïnvloeden hoe hard de inktlaag wordt of hoe gevoelig de opgedroogde inkt is voor water of zure vloeistoffen. Ook de lengte van de polymeren kunnen we variëren, dat geeft ook andere eigenschappen”, zegt Metselaar. We lopen ondertussen naar het laboratorium waar al die mogelijke variaties in de praktijk worden gebracht.
Ik ben inmiddels heel benieuwd hoe zo’n bindmiddel eruitziet en kijk vol verwachting in de reactiekolven die in verschillende zuurkasten staan. Gerald Metselaar vult mijn gedachten feilloos in. “Niet heel spannend hè, het ziet er allemaal uit als melk.” De dispersies – de vakterm voor een vloeistof waarin heel kleine deeltjes zijn verspreid, maar niet opgelost – zijn allemaal wit omdat de kleine polymeerbolletjes in beweging zijn en al het licht even sterk reflecteren naar alle kanten. “Daardoor zie je een witte vloeistof, maar als je dit in een dunne laag laat drogen heb je een volledige transparante coating”, zegt Metselaar. Daar kun je moeilijk iets aan zien als je de effecten in de uiteindelijke inkt wilt bepalen.
Cadeaupapier
De oplossing: je gaat het gebruik van het bindmiddel nabootsen door zelf inkt te maken en die te gebruiken. Dat is de rol van het tweede laboratorium dat we bezoeken, het applicatielab. Hier knallen de kleuren je tegemoet. Aan de bindmiddelen wordt een pigment toegevoegd en dan kun je bijvoorbeeld goed zien hoe de kleur uitpakt als je het in een dun laagje op een plastic folie uitrolt. En zo zijn er nog veel meer mogelijkheden om de performance van het bindmiddel te testen.
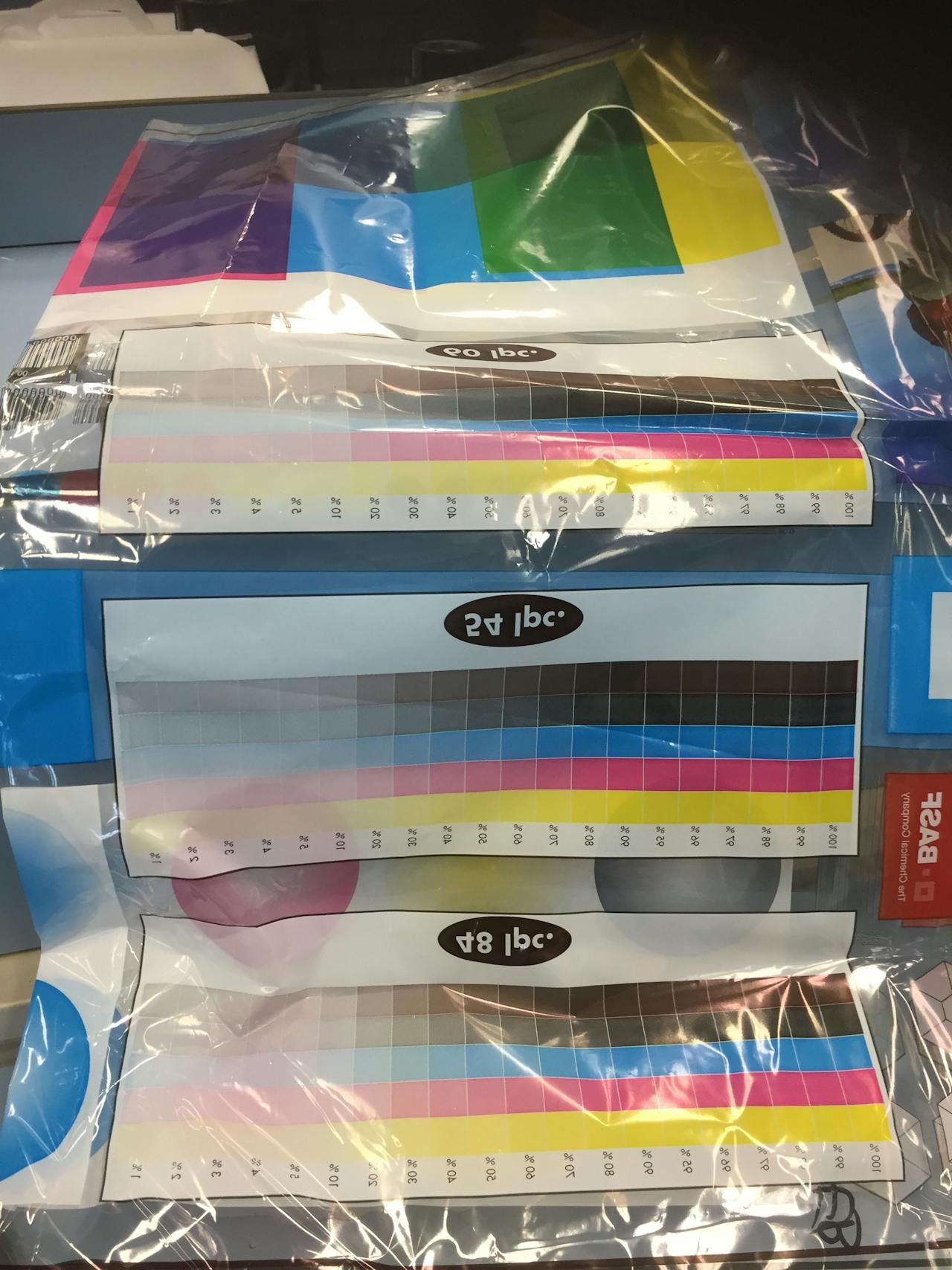
Door zelf de folie te bedrukken, kunnen de ontwikkelaars van BASF zien hoe de inkt op basis van hun ingrediënten uiteindelijk oogt.
Esther Thole voor NEMO KennislinkEigenlijk is dit lab een heel compacte weergave van de wereld waarin de producten van BASF straks terechtkomen. Er staan allerlei bijzondere apparaten, zoals een metalliseermachine. “Hiermee kunnen we papier metalliseren, dat betekent dat je er een heel dun laagje aluminium op aanbrengt”, licht Arjan Termaten toe. “Gemetalliseerd papier kom je tegen als cadeaupapier of in decoratieve verpakkingen.” Ook daar worden weer patronen op gedrukt met, je raadt het al, inkt. Zo kunnen ze testen hoe een nieuwe inkt zich gedraagt op dit type papier. Snel een cadeautje inpakken voor een jarige collega zal hier geen probleem zijn.
Mini-drukkerij
In een aparte kamer in de hoek van het lab staat een uit de kluiten gewassen apparaat dat door Metselaar en Termaten liefkozend ‘de Moser’ wordt genoemd. Het is een heuse drukpers in een eigen mini-drukkerij. Ook dit is een voorbeeld van hoe de ontwikkelaars uitzoeken of hun aangepaste bestanddelen goed werken. Stellingkasten vol rollen transparante folie vol met kleurige vakjes van verschillende intensiteit laten zien dat hier heel wat af gedrukt wordt. Steeds maar proberen hoe de melkachtige oplossingen uit het synthese lab zich gedragen in de echte wereld van de drukkerij. Met al die aangepaste inkt lijkt de Moser geen moeite te hebben. Die draait al bijna 25 jaar mee, zie ik op het plaatje. “Echt een voorbeeld van Duitse degelijkheid”, lacht Termaten. “Deze spullen gaan gewoon niet kapot.” Een baken van stabiliteit dat zich niet van de wijs laat brengen door steeds net iets andere minuscule bolletjes.